Researchers at City University of Hong Kong (CityU) have demonstrated large, uniform tensile elastic straining of microfabricated diamond arrays through the nanomechanical approach. This has the potential of strained diamonds as prime candidates for advanced functional devices in microelectronics, photonics, and quantum information technologies.
Above – CAPTION Stretching of microfabricated diamonds pave ways for applications in next-generation microelectronics. CREDIT Dang Chaoqun / City University of Hong Kong
Diamond has a high-performance electronic and photonic material due to its ultra-high thermal conductivity, exceptional electric charge carrier mobility, high breakdown strength and ultra-wide bandgap. Bandgap is a key property in semi-conductor, and wide bandgap allows operation of high-power or high-frequency devices.
Science – Achieving large uniform tensile elasticity in microfabricated diamond
Stretching diamond to the limit
Diamond is thought of as being unbendable, but thin samples can actually deform elastically. Applying relatively large amounts of strain to diamond may shift its electronic properties, which is of interest for a number of applications. Dang et al. elastically stretched micrometer-sized plates of diamond along different crystallographic directions. These relatively large samples show that deep-strain engineering can be accomplished in more uniform diamond specimens and may have a large impact on the electronic properties.
Abstract
Diamond is not only the hardest material in nature, but is also an extreme electronic material with an ultrawide bandgap, exceptional carrier mobilities, and thermal conductivity. Straining diamond can push such extreme figures of merit for device applications. We microfabricated single-crystalline diamond bridge structures with ~1 micrometer length by ~100 nanometer width and achieved sample-wide uniform elastic strains under uniaxial tensile loading along the [100], [101], and [111] directions at room temperature. We also demonstrated deep elastic straining of diamond microbridge arrays. The ultralarge, highly controllable elastic strains can fundamentally change the bulk band structures of diamond, including a substantial calculated bandgap reduction as much as ~2 electron volts. Our demonstration highlights the immense application potential of deep elastic strain engineering for photonics, electronics, and quantum information technologies.
Uniform tensile straining across the sample
The team firstly microfabricated single-crystalline diamond samples from a solid diamond single crystals. The samples were in bridge-like shape – about one micrometre long and 300 nanometres wide, with both ends wider for gripping (See image: Tensile straining of diamond bridges). The diamond bridges were then uniaxially stretched in a well-controlled manner within an electron microscope. Under cycles of continuous and controllable loading-unloading of quantitative tensile tests, the diamond bridges demonstrated a highly uniform, large elastic deformation of about 7.5% strain across the whole gauge section of the specimen, rather than deforming at a localized area in bending. And they recovered their original shape after unloading.
By further optimizing the sample geometry using the American Society for Testing and Materials (ASTM) standard, they achieved a maximum uniform tensile strain of up to 9.7%, which even surpassed the maximum local value in the 2018 study, and was close to the theoretical elastic limit of diamond. More importantly, to demonstrate the strained diamond device concept, the team also realized elastic straining of microfabricated diamond arrays.
Tuning the bandgap by elastic strains
The team then performed density functional theory (DFT) calculations to estimate the impact of elastic straining from 0 to 12% on the diamond’s electronic properties. The simulation results indicated that the bandgap of diamond generally decreased as the tensile strain increased, with the largest bandgap reduction rate down from about 5 eV to 3 eV at around 9% strain along a specific crystalline orientation. The team performed an electron energy-loss spectroscopy analysis on a pre-strained diamond sample and verified this bandgap decreasing trend.
SOURCES- City University of Hong Kong, Science
Written By brian Wang, Nextbigfuture.com
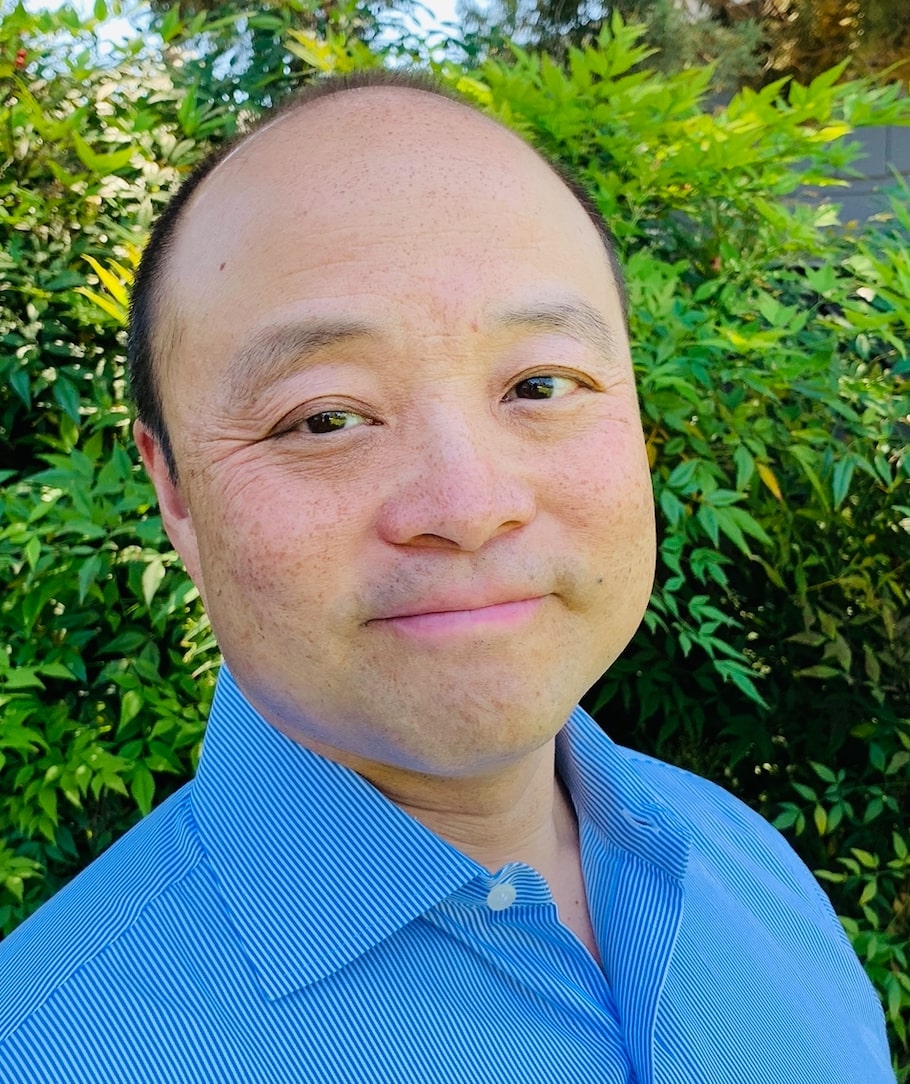
Brian Wang is a Futurist Thought Leader and a popular Science blogger with 1 million readers per month. His blog Nextbigfuture.com is ranked #1 Science News Blog. It covers many disruptive technology and trends including Space, Robotics, Artificial Intelligence, Medicine, Anti-aging Biotechnology, and Nanotechnology.
Known for identifying cutting edge technologies, he is currently a Co-Founder of a startup and fundraiser for high potential early-stage companies. He is the Head of Research for Allocations for deep technology investments and an Angel Investor at Space Angels.
A frequent speaker at corporations, he has been a TEDx speaker, a Singularity University speaker and guest at numerous interviews for radio and podcasts. He is open to public speaking and advising engagements.
I agree that it's a stupid measure, but it's a traditional stupid measure.
Human hair widths are generally between 17 and 180 micrometers, making it a particularly bad metric for any comparison. At least use something consistent, like the thickness of a credit card, then they can actually hold one in their hand for reference.
They have been talking about replacing silicon with diamonds for many years.
Yes, diamond makes for a superior semiconductor, but obviously there are constraints.
Doesn't that reverse the effect of multiple strands?
If it's all one strand running through pulleys, then a break anywhere on any of the strands leads to the whole thing running through the pulleys and coming apart.
A friend of mine proposed dealing with the problem of cable taper on a sky hook, by running a uniform cable through pulley sheaves. At each height you'd simply have the cable wrapped around the necessary number of times to handle the load.
Using his scheme, you could have a single pass system, a cable factory at the base, and at the counterweight you treat the used cable as raw material for building less highly stressed stuff.
Some sort of incorrect significant figures thinking? Trying to keep it to 3 digits or less, and avoid decimals.
A single nanotube would normally have elastic (brittle) failure (unless it rearranges as Brett says, and then you remove the stress just before it snaps). But with a bundle of them, you could possibly chemically tune them to allow some slippage. That should produce plastic deformation. If you tune it just right, you might not reduce the maximum stress much, either (but AFAIK that hasn't been achieved yet, so currently it's just hand waving).
Didn't bother me, I just converted automatically. They are both really the same unit: meter.
East Asian, African or European hair?
I suspect that you could do something if the half life is larger than the service life of each component.
Once you've got the space elevator operational, it should be cheap to send up replacement bits of cable. Then you can replace them fairly easily assuming you have multiple parallel strands of cable between each node. You replace them one at a time so you've only ever removed 10% of the total load bearing structure at any one point in time.
Note: You would need to do that anyway because of micrometeoroid damage.
The problem they've seen with nanotubes at comparable strain levels is that the molecule becomes metastable; While it can hold against the strain for a while, it's got a half-life, because it can tunnel through to a lower energy configuration.
For stability you need the energy required to break to be more than the energy stored locally in the structure. Crack propagation needs to consume, not liberate, energy.
We'll occasionally compare things to the width of a human hair where I work, but only when trying to get non-technical people to understand the scale of our work. (Because our stamping tolerances are generally on that order, or less.)
Non-technical people tend not to have a feel for the size of a micron. But there's still no excuse for mixing units like that.
I'm just glad they didn't throw in 1 micrometre long and 12 millionths of an inch wide.
Or start measuring things in widths of a human hair, which is another common failure mode whenever people start talking about small things.
No, that fails with a bang issue (i.e. brittle failure by cracking) means you'd
But pretty much anything we've ever looked at that could take that sort of load would behave in a similar fashion.
Even if you can get the diamond up to 9.7% strain without it instantly breaking, it probably won't be very stable in a cable application.
This does suggest that diamond strain sensors could be very sensitive, though.
My main squeeze, Peizo, would smile.
"about one micrometre long and 300 nanometres wide" Seriously, would it that hard to say, "About 1000 nm long and 300 nm wide", and NOT MIX UNITS? I'd have been fine even with, "About one micrometre long and a third of a micrometre wide".
That's the standard materials engineering use of the term.
Elastic strain is distorting the material, but not to the point of producing any permanent change (such as changing the bond connections).
Plastic strain is when you start to change the bond connections.
Because of diamond's structure, you can't really get the bonds to switch to a new connection just by mechanical stress, so when the old connection reaches its limits, it just fails with a bang.
I've seen a few theoretical analyses and they concluded that a simple crystalline structure (they were looking at metals) really can't go beyond about 10% elastic strain, even if it is theoretically perfect on an atomic scale, so to get real material samples to 9.7% is really pushing it.
And remember, the elastic modulus of diamond (the theoretical load to stretch it 100%) is 1143 GPa, so reaching 9.7% of that is 111 GPa which is well and truly into Space elevator territory.
Though 1 micrometre in length is not in space elevator sizes. Still, a simple matter of scaling it up over 15 orders of magnitude. The fusion reactor boys do that all the time.
Can you buy one for a ring?
The word "strain" must be in the context of crystals, stress or distort not to the point of changing the bond connections. Seems a little strange, tho.