DUPIC stands for Direct Use of Pressurized Water Reactor Spent Fuel in CANDU. CANDU is the Canadian heavy water nuclear reactor. (H/T David Walters
DUPIC Costs
The extra cost of DUPIC has been estimated to be six to ten percent above the once-through cost. This is far below credible estimates for the cost of the fast-reactor fuel cycle, which started at 25 percent above once-through. Moreover, there are many CANDU reactors operating around the world, with excellent in-service records. Their operating costs are well known, and competitive with those of light water reactors.
DUPIC Advantages and Technical Issues
The DUPIC technique has certain advantages:
No materials are separated during the refabrication process. Uranium, plutonium, fission products and minor actinides are kept together in the fuel powder and bound together again in the DUPIC fuel bundles.
* A high net destruction rate can be achieved of actinides and plutonium.
* Up to 25% more energy can be realised compared to other PWR used fuel recycling techniques.
* And a DUPIC fuel cycle could reduce a country¹s need for used PWR fuel disposal by 70% while reducing fresh uranium requirements by 30%.
Used nuclear fuel is highly radioactive and generates heat. This high activity means that the DUPIC manufacture process must be carried out remotely behind heavy shielding. While these restrictions make the diversion of fissile materials much more difficult and hence increase security, they also make the manufacture process more complex compared with that for the original PWR fuel, which is barely radioactive before use.
Canada, which developed the CANDU reactor, and South Korea, which hosts four CANDU units as well as many PWRs, have initiated a bilateral joint research program to develop DUPIC and the Korean Atomic Energy Research Institute (KAERI) has been implementing a comprehensive development program since 1992 to demonstrate the DUPIC fuel cycle concept.
KAERI believes that although it is too early to commercialise the DUPIC fuel cycle, the key technologies are in place for a practical demonstration of the technique. Challenges which remain include the development of a technology to produce fuel pellets of the correct density, the development of remote fabrication equipment and the handling of the used PWR fuel. However, KAERI successfully manufactured DUPIC small fuel elements for irradiation tests inside the HANARO research reactor in April 2000 and fabricated full-size DUPIC elements in February 2001. AECL is also able to manufacture DUPIC fuel elements.
Research is also underway on the reactor physics of DUPIC fuel and the impacts on safety systems.
A further complication is the loading of highly radioactive DUPIC fuel into the CANDU reactor. Normal fuel handling systems are designed for the fuel to be hot and highly radioactive only after use, but it is thought that the used fuel path from the reactor to cooling pond could be reversed in order to load DUPIC fuel, and studies of South Korea’s Wolsong CANDU units indicate that both the front- and rear-loading techniques could be used with some plant modification.
Used fuel from light water reactors (at normal US burn-up levels) contains approximately:
95.6% uranium (U-232: 0.1-0.3%; U-234: 0.1-0.3%; U-235: 0.5-1.0%; U-236: 4-0.7%; balance: U-238)
2.9% stable fission products
0.9% plutonium
0.3% caesium & strontium (fission products)
0.1% iodine and technetium (fission products)
0.1% other long-lived fission products
0.1% minor actinides (americium, curium, neptunium)
South Korea Nuclear Power
South Korea is now moving toward a full 60% of electricity capacity from Nuclear power (versus 40% now), which could put them close to 75% of real generation. They have now 5 1 GW-plus reactors under construction and 3 more planned to start over the next 5 years. These 3 including the last one that was started in the fall of last year, is the APR-1400, a 1350 MW ingeniously built, partially Korean designed nuclear power plant based on a Generation III+ reactor originally conceived by, but never implement by, Westinghouse on a NRC approved design known as “System 80+”.
The Koreans are also working on advanced reprocessing facilities to recover the 97% of the energy that sits in spent nuclear fuel facilities.
DUPIC Status Report from 2006
6 page DUPIC status report from 2006
The Korea Atomic Energy Research Institute (KAERI) established the DUPIC fuel development facility (DFDF) in 1999 to process the PWR spent fuel and to
fabricate the DUPIC fuel on a laboratory scale. In this facility, about 25 pieces of fuel fabrication equipment are installed. (Lab scale facility)
1) Decladding machine, OREOX furnace, off-gas treatment system, attrition mill and mixer to produce
DUPIC fuel powder from the PWR spent fuel
2) Compaction press, high temperature sintering furnace, center-less grinder, pellet cleaner and dryer,
pellet stack length adjuster and pellet loader to fabricate DUPIC fuel pellets
3) Remote laser welder and welding chamber to fabricate DUPIC fuel elements
4) Quality inspection devices to characterize the DUPIC fuel powder, pellets and elements.
KAERI fabricated real size DUPIC fuel elements in February 2001.
A comparison of the optical microscopy photos showed that the irradiation
behavior of the DUPIC fuel is similar to that of the standard CANDU spent fuel or PWR spent fuel of 40000 MWd/tHM.
The engineering-scale DUPIC facility will be designed with a capacity of 50 ton/yr and a plant lifetime of 40 yrs. The design also considers the expansion of the facility to a commercial-scale plant. The main process building is located in the centre, surrounded by auxiliary buildings such as a utility facility, health physics buildings, etc. The overall process can be categorized into a DUPIC fuel fabrication, a structural part recycling and a radioactive waste treatment. A detailed flow path of the main processes is as follows:
– PWR spent fuel receiving and storage
– Spent fuel disassembly and decladding (99% recovery of the fuel material from the clad)
– Fuel powder preparation by the OREOX process
– Fuel pellet fabrication with a theoretical density of more than 95%
– Fuel rod fabrication including a surface decontamination and fissile content measurement.
– Fuel bundle fabrication in the CANFLEX geometry.
Though it is yet too early to launch the commercialization of the DUPIC fuel based on the basic DUPIC fuel technologies developed until now, it is also true that the key technologies have been developed for the DUPIC fuel cycle. Therefore it is expected that there should be no technical problems to develop the commercial DUPIC fuel technology once the DUPIC fuel technology and its performance are demonstrated through a practical use of the DUPIC fuel, which will be an extremely important turning point in the history of nuclear power development. By utilizing spent fuel by an internationally-proven proliferation-resistant technology, it is expected that the burden of a spent fuel accumulation will be relieved not only in the domestic nuclear grid but also in the worldwide nuclear power industry.
Electrolytic/electrometallurgical processing techniques (‘pyroprocessing’) to separate nuclides from a radioactive waste stream have been under development in the US Department of Energy laboratories, notably Argonne, as well as by the Korea Atomic Energy Research Institute (KAERI) in conjunction with work on DUPIC
The KAERI advanced spent fuel conditioning process (ACP) involves separating uranium, transuranics including plutonium, and fission products including lanthanides. It utilises a high-temperature lithium-potassium cathode. Development of this process is at the heart of US-South Korean nuclear cooperation, and will be central to the renewal of the bilateral US-South Korean nuclear cooperation agreement in 2014, so is already receiving considerable attention in negotiations.
With US assistance through the International Nuclear Energy Research Initiative (I-NERI) program KAERI built the Advanced Spent Fuel Conditioning Process Facility (ACPF) at KAERI in 2005. KAERI hopes the project will be expanded to engineering scale by 2012, leading to the first stage of a Korea Advanced Pyroprocessing Facility (KAPF) starting in 2016 and becoming a commercial-scale demonstration plant in 2025
FURTHER READING
Older 6 page report on Korea’s DUPIC plans
Canada nuclear yearbook for 2008. 54 pages
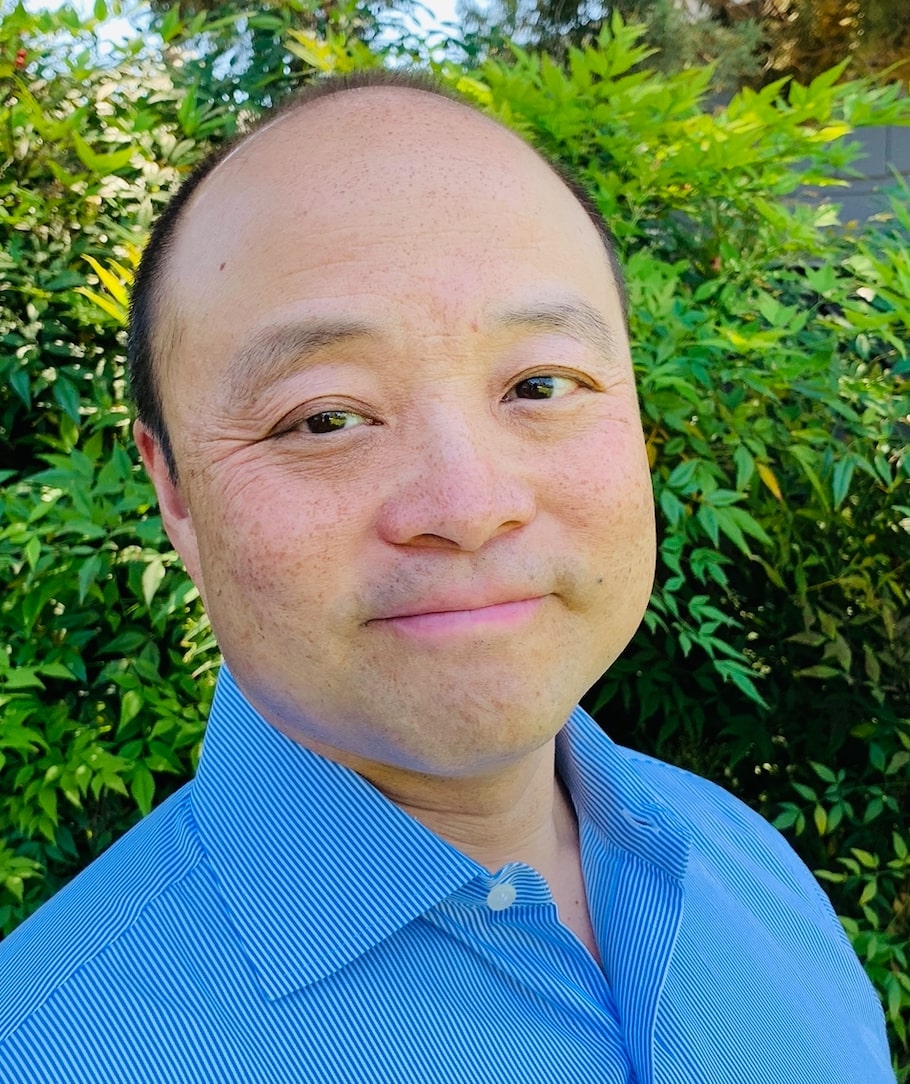
Brian Wang is a Futurist Thought Leader and a popular Science blogger with 1 million readers per month. His blog Nextbigfuture.com is ranked #1 Science News Blog. It covers many disruptive technology and trends including Space, Robotics, Artificial Intelligence, Medicine, Anti-aging Biotechnology, and Nanotechnology.
Known for identifying cutting edge technologies, he is currently a Co-Founder of a startup and fundraiser for high potential early-stage companies. He is the Head of Research for Allocations for deep technology investments and an Angel Investor at Space Angels.
A frequent speaker at corporations, he has been a TEDx speaker, a Singularity University speaker and guest at numerous interviews for radio and podcasts. He is open to public speaking and advising engagements.