Researchers at MIT’s Research Laboratory of Electronics and Singapore’s Engineering Agency for Science, Technology and Research (A*STAR) have demonstrated a new technique that could produce chip features only 10 nanometers — or about 30 atoms — across. The researchers use existing methods to deposit narrow pillars of plastic on a chip’s surface; then they cause the pillars to collapse in predetermined directions, covering the chip with intricate patterns.
Journal Small – Controlled Collapse of High-Aspect-Ratio Nanostructures
Schematics of nanogap formation by collapsing curved linear HAR structures, where h is the height of structures, p is the separating distance between two adjacent structures, and d is the nanogap size after the collapse of structures.
In the first of the two papers, published last year in the journal Nano Letters, Berggren and Huigao Duan, a visiting student from Lanzhou University in China, showed that when two pillars are very close to each other, they will collapse toward each other. In a follow-up paper, appearing in the Sept. 5 issue of the nanotech journal Small, Berggren, Duan (now at A*STAR) and Joel Yang (who did his PhD work with Berggren, also joining A*STAR after graduating in 2009) show that by controlling the shape of isolated pillars, they can get them to collapse in whatever direction they choose.
More particularly, slightly flattening one side of the pillar will cause it to collapse in the opposite direction. The researchers have no idea why, Berggren says: When they hatched the idea of asymmetric pillars, they expected them to collapse toward the flat side, the way a tree tends to collapse in the direction of the axe that’s striking it. In experiments, the partially flattened pillars would collapse in the intended direction with about 98 percent reliability. “That’s not acceptable from an industrial perspective,” Berggren says, “but it’s certainly fine as a starting point in an engineering demonstration.”
At the moment, the technique does have its limitations. Space the pillars too close together, and they’ll collapse toward each other, no matter their shape. That restricts the range of patterns that the technique can produce on chips with structures packed tightly together, as they are on computer chips.
But according to Joanna Aizenberg, the Amy Smith Berylson Professor of Materials Science at Harvard University, the applications where the technique will prove most useful may not have been imagined yet. “It can open the way to create structures that were just not possible before,” Aizenberg says. “They’re not in manufacturing yet because nobody knew how to make them.”
Although Berggren and his colleagues didn’t know it when they began their own experiments, for several years Aizenberg’s group has been using the controlled collapse of structures on the micrometer scale to produce materials with novel optical properties. But “particularly interesting applications would come from this sub-100-nanometer scale,” Aizenberg says. “It’s a really amazing level of control of the nanostructure assembly that Karl’s group has achieved.”
Capillary-force-induced collapse of high-aspect-ratio (HAR) micro- and nanostructures is common in the evaporation–drying process and a number of applications based on the collapse have been proposed. However, the collapse of small HAR structures is usually uncontrollable, which has prevented it from being used in engineering applications. Here, the collapse of 10-nm-scale structures is separately controlled through engineering an asymmetric cross section, curvature, and tilt in the structures prior to collapse. It is shown that this deterministic-collapse approach can be used to create linear structures from collapsed pillars and planar rectangular structures from collapsed fencelike linear structures, and can further be used to create small gaps by controlling the collapse of nearby structures. These techniques could be used to improve the performance of beam-based lithography methods for certain types of patterns by increasing throughput and resolution, reducing the proximity effect, and reducing irradiation damage. In addition, this controlled-collapse concept provides a possible platform with which to study mechanical behavior at the 10-nm scale.
16 pages of supplemental information
If you liked this article, please give it a quick review on ycombinator or StumbleUpon. Thanks
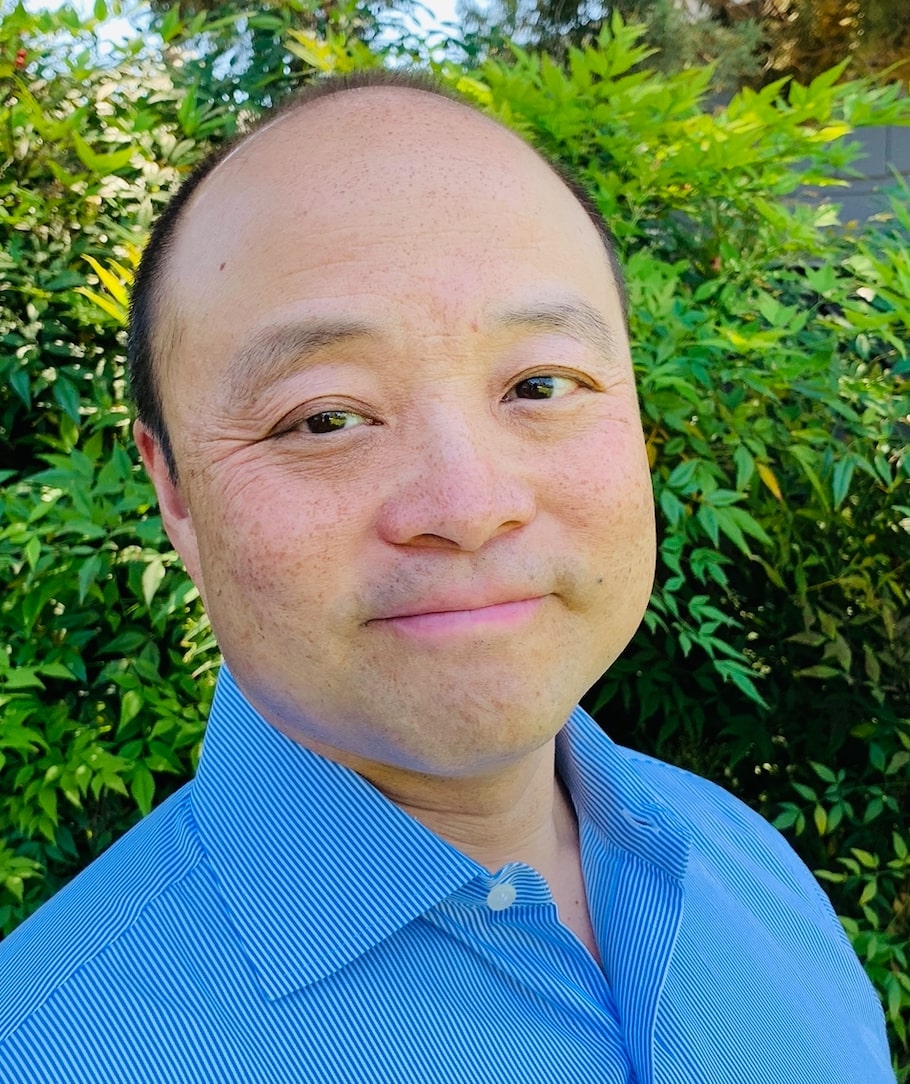
Brian Wang is a Futurist Thought Leader and a popular Science blogger with 1 million readers per month. His blog Nextbigfuture.com is ranked #1 Science News Blog. It covers many disruptive technology and trends including Space, Robotics, Artificial Intelligence, Medicine, Anti-aging Biotechnology, and Nanotechnology.
Known for identifying cutting edge technologies, he is currently a Co-Founder of a startup and fundraiser for high potential early-stage companies. He is the Head of Research for Allocations for deep technology investments and an Angel Investor at Space Angels.
A frequent speaker at corporations, he has been a TEDx speaker, a Singularity University speaker and guest at numerous interviews for radio and podcasts. He is open to public speaking and advising engagements.