A team including scientists at the National Institute of Standards and Technology (NIST) may have overcome a significant hurdle to manufacturing hydrogen fuel cells by creating a way to check whether the expensive catalysts the cells need have been incorporated quickly and effectively. Improved measurement methods are key to bringing hydrogen power a step closer to economical mass production.
Above – Well-controlled illumination allows the team’s prototype device (top left) to scan thin layers of liquid containing platinum nanoparticles (lower center), a catalyst used in fuel cells. Scaling up the approach (right) could help meet industry’s quality-control needs.
Credit: M. Stocker / NIST
Hydrogen vehicles have not conquered the road like electric ones have yet, but it’s not for lack of efficiency or environmental friendliness. Hydrogen gas contains about three times as much energy by mass as fossil fuels do, and a fuel cell’s only byproduct is water. But, while filling a fuel tank with hydrogen is fast, building the engine is not, at least by industrial standards. A fuel cell requires thin layers of a platinum-based catalyst to convert hydrogen into electric energy, and the industry has lacked an efficient way to evaluate the layers’ properties. That lack is one reason only about 1,800 hydrogen vehicles (link is external) were on the road as of a year or so ago, and they can cost twice as much as a conventional vehicle.
The catalyst needs to end up as two thin layers on either side of a polymer sheet that resembles plastic wrap, so the industry’s approach has been to treat the catalyst like ink. The process mixes platinum particles with carbon to form a deep black fluid that even looks ink-like. Then a machine resembling a newspaper printing press lays the mixture down as the sheet unspools from a giant roll. The problem is that the platinum in this ink costs upwards of $35 per gram ($1,000 an ounce), so manufacturers need a way to make sure just enough is laid down to get the job done—and not one costly drop more. And the process has to be fast enough to make fuel cells for thousands of cars per year, meaning the plastic has to roll quickly.
The team, which included scientists from NIST and industry, found an answer stemming from their experience measuring small objects for a completely different industry: computer chip manufacturing. But their usual approach, based on reflecting a laser’s light from a chip surface, demanded a rethink.
“We’ve got expertise in optical methods for measuring features smaller than 10 nanometers on chips, and the platinum particles are at the same scale,” said NIST physical scientist Michael Stocker. “We knew basically what we were doing, but chips don’t fly by at 30 meters (about 100 feet) per minute, so there was a speed challenge. Plus, you’re looking at something that’s black, so we didn’t have much reflected light to measure.”
After addressing this challenge through research and development, the team built a novel instrument using off-the-shelf technology that can detect the low levels of light reflected off the tiny platinum particles as the sheet moves past at a meter or two per minute.
Stocker said there are no fundamental barriers to scaling up the method or increasing the speed to meet the industry’s future needs. For instance, a manufacturer could array a row of these instruments to scan a meter-wide sheet, with each one identifying trouble spots in a particular section. Though the method would likely need to be combined with other techniques such as X-ray fluorescence to form a complete solution, Stocker said that it leaves fuel cell manufacturers in a good place.
“It’s all just optical engineering from this point onward,” he said. “Industry can take it from here.”
Highlights
• Visible-light optical reflection is proposed as a viable catalyst-loading monitor.
• Three optical methods are qualitatively sensitive to Pt loading on MEA soft goods.
• A new optical tool tailored for fuel cell manufacturing is dynamically demonstrated.
• Quantitative analysis yields sub-0.01 mg/cm2 sensitivities to Pt loading change.
Abstract
Widespread commercialization of proton exchange membrane fuel cells remains curbed by various manufacturing and infrastructure challenges. One such technical barrier identified by the U. S. Department of Energy is the need for high-speed, in-line process control of platinum-based catalyst layers in the membrane electrode assembly of the fuel cell. Using multiple reflectivity-based optical methods, such as optical scatterometry and large aperture projection scatterometry, we demonstrate in-line-capable catalyst loading measurements of carbon-supported Pt nanoparticle and Pt-alloy nanostructured thin film catalyst coated membranes. Large aperture projection scatterometry is a new high-throughput approach developed at the National Institute of Standards and Technology specifically for fuel cell manufacturing metrology. Angle- and wavelength-resolved measurements of these fuel cell soft goods validate the ability of reflectivity-based measurements to produce industrially relevant sensitivities to changes in Pt and Pt-alloy loading. The successful application of these optical methods to fuel cell manufacturing metrology directly addresses the shortage of high-throughput process control approaches needed to facilitate performance improvements and manufacturing cost-reductions required to make fuel cells commercially viable.
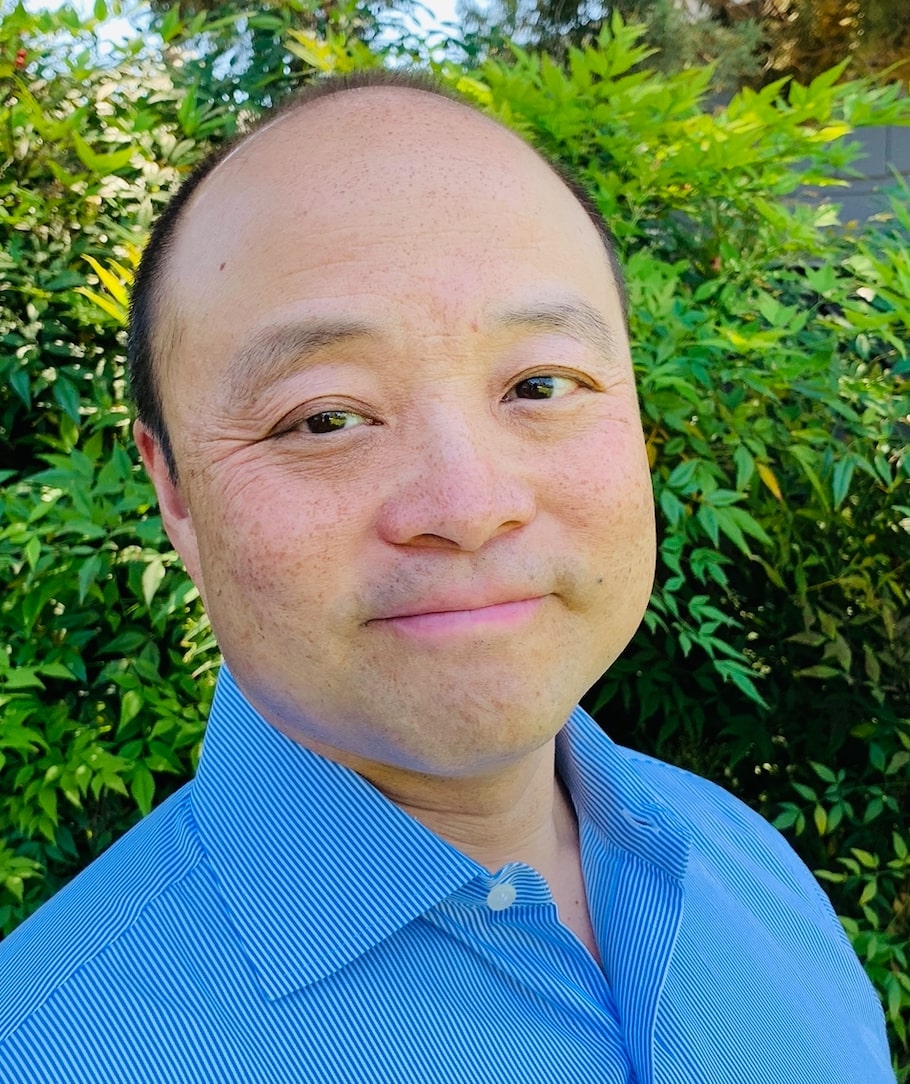
Brian Wang is a Futurist Thought Leader and a popular Science blogger with 1 million readers per month. His blog Nextbigfuture.com is ranked #1 Science News Blog. It covers many disruptive technology and trends including Space, Robotics, Artificial Intelligence, Medicine, Anti-aging Biotechnology, and Nanotechnology.
Known for identifying cutting edge technologies, he is currently a Co-Founder of a startup and fundraiser for high potential early-stage companies. He is the Head of Research for Allocations for deep technology investments and an Angel Investor at Space Angels.
A frequent speaker at corporations, he has been a TEDx speaker, a Singularity University speaker and guest at numerous interviews for radio and podcasts. He is open to public speaking and advising engagements.
Blah blah blah… Hydrogen contains three times as much energy by mass as fossil fuels do…
Nobody cares.
Oh it matters for space ships, but on the road? There is not one road vehicle in production where the mass of the fuel in the fuel tank is of any significance.
Well maybe actual petrol tanker trucks. But there the huge volume means they would carry less energy per truck anyway, even if the actual fuel load was lighter. Ignoring the weight of a hydrogen tank.
Every article of hydrogen cars mentions this, and it just makes it look like they have nothing real to offer. A classic case of damning with faint praise.
I’m reminded of an article I read this morning about using nitrous oxide in racing. And, as ALWAYS, they mention “nitrous oxide is 36% oxygen by weight, while air is only 20%. So it has 1.8 times the oxygen”. And as always this shows that the author knows nothing about how it works. Air (or nitrous) is inducted by volume (= number of molecules), not mass. What matters is that nitrous has 1 oxygen atom per molecule, while air has only 0.4. So it actually has 2.5 times the oxygen if you know wtf you are talking about.