Breakthrough Starshot has been provided $100 million in funding and currently has precursor chipsats in orbit.
Nanocrafts
Nanocrafts are gram-scale robotic spacecrafts comprising two main parts:
StarChip: Moore’s law has allowed a dramatic decrease in the size of microelectronic components. This creates the possibility of a gram-scale wafer, carrying cameras, photon thrusters, power supply, navigation and communication equipment, and constituting a fully functional space probe.
Lightsail: Advances in nanotechnology are producing increasingly thin and light-weight metamaterials, promising to enable the fabrication of meter-scale sails no more than a few hundred atoms thick and at gram-scale mass.
Light Beamer
The rising power and falling cost of lasers, consistent with Moore’s law, lead to significant advances in light beaming technology. Meanwhile, phased arrays of lasers (the ‘light beamer’) could potentially be scaled up to the 100 gigawatt level.
Breakthrough Starshot aims to bring economies of scale to the astronomical scale. The StarChip can be mass-produced at the cost of an iPhone and sent on missions in large numbers to provide redundancy and coverage. The light beamer is modular and scalable.
Lightsail
Breakthrough starshot is consider a laser beam in the 100 GW class. If, for example, one one hundred thousandth of the energy is absorbed by a 4 meterx4 meter sail, it will be heated by about 60kW per m2, which is roughly 60 times more than sunlight illumination on Earth. This will heat the material but not melt it. Using fully dielectric sails, they can reduce the absorption to less than one billionth of the beamed energy for optimized materials.
Two possible approaches to mitigate the heating challenge have been identified:
1. High reflectivity
Use a material with better than 99.999% reflectivity. Usually, highly reflective surfaces are dielectric mirrors, which are composed of ‘sandwiches’ of material, with each layer reflecting back a modest fraction of the total. Each layer needs to be at least a quarter of a wavelength thick. The weight can be reduced by using a monolayer with high reflectivity at the correct wavelength. Based on recent research, this could be achieved by a ‘hole-pocked’ layer, highly reflective for very specific angles where reflectivity caustics arise. (These caustics occur for wavelengths of light that are actually longer than the sheet thickness.) Adding the holes serves a dual purpose; it reduces the weight of the sail and it could greatly increase reflectivity. This is but one possibility being explored. Modern materials research will explore new materials such as graphene; Breakthrough Starshot aims to take advantage of this rapidly advancing field. The basic Starshot system allows a wide range of options for nanocraft masses and capabilities, all using the same array. This gives it great flexibility in optimizing the science and technology roadmaps.
2. Low absorption
Use a material (such as glass) that has a very low absorption coefficient even when not highly reflective. Such materials are used in fiber optics systems with high power applications. Without the protection of a highly reflective sail, the StarChip electronics would need to be protected from the incoming flux. But this could be accomplished by a combination of geometry (orienting the electronics ‘sideways’ with a low cross-section) and placing a very highly reflective coating only on the sensitive components. These can use the multi-layer dielectric approaches mentioned above, which have already been demonstrated in the lab. Using low absorption sail material, together with a limited use of high-reflectivity shielding for critical electronics, would protect the StarChip without increasing its mass beyond the gram scale. There are a number of high-reflectivity, low absorption materials in existence. For possible fabrication and verification, a demonstrable design of silicon microcubes on a silicon dioxide substrate is under consideration.
As demonstrated by the Japanese IKAROS mission, spinning the sail can reduce wrinkles on its surface. Special attention is needed to avoid impurities and non- uniformities in the sail composition – for example, near mechanical attachments – or accumulation of dust particles on its surface, which could otherwise lead to a localized deposition of energy. There are a wide variety of options allowing optimization of the sail design.
Pete Klupar, Breakthrough Starshot’
Silicon can be made very thin, a few atoms thick, also although silicon is brittle we could have these pyramids of silicon bonded to the back of a much more flexible optical glass material. Now if we leave a very small space between the pyramids so that light has great trouble moving through it we could have great reflectivity with great flexibility. Pyramids offer reduced weight for their thickness, a 1.6 micron thick layer of pyramids has the mass of roughly 1/3 that of the same planar thickness of material.
We report the fabrication of micro/nanoscale pits with facile shape, orientation, and size controls on an Si surface via an Au-nanoparticles-assisted vapor transport method. The pit dimensions can be continuously tuned from 70 nm to several μm, and the shapes of triangles, squares, and wire/hexagons are prepared on Si (111), (100), and (110) substrates, respectively. This reliable shape control hinges on the anisotropic diffusivity of Co in Si and the sublimation of cobalt silicide nanoislands. The experimental conditions, in particular the substrate orientation and the growth temperature, dictate the pit morphology. On the basis of this understanding of the mechanism and the morphological evolution of the pits, we manage to estimate the diffusion coefficients of Co in bulk Si along the ⟨100⟩ and ⟨111⟩ directions, that is D100 and D111. These diffusion coefficients show strong temperature dependence, for example, D100 is ca. 3 times larger than D111 at 860 °C, while they approach almost the same value at 1000 °C. This simple bottom-up route may help to develop new technologies for Si-based nanofabrication and to find potential applications in constructing nanodevices.
By firing kinetic sails into comets or asteroids we could refine the sails control systems to a greater accuracy while working on our Starshot concept, sort of ironing out the details but at the same time providing benefits on the go. They are considering this in the second phase of our project which we call the prototype phase. We anticipate this to begin sometime in the 2020’s.
– Pete Klupar, Breakthrough Starshot
Other Technical Challenges that are being studied
Gram-scale StarChip components | 4 photon thrusters
Sub-gram scale 1W diode lasers are currently widely available at very low costs. The manufacturing trend has seen power double for the same mass every two years. It is anticipated this trend will continue for these devices for some time.
Gram-scale StarChip components | 4 cameras
Sub-gram-scale 2 megapixel cameras are currently widely available at very low costs. The trend has been a doubling of pixels for the same mass every two years.
Gram-scale StarChip components | 4 processors
Sub-gram scale microprocessors are currently widely available at very low costs. The trend has been a doubling of processor count for the same mass every two years. It is anticipated that these devices will continue this trend for some time.
Gram-scale StarChip components | Battery
Battery design is one of the most challenging aspects of the mission. Currently under consideration for the energy source onboard are plutonium-238, which is in common use, or Americium-241. 150mg has been allocated for the mass of the battery. This includes the mass of the radioisotope and the ultra-capacitor.
Gram-scale StarChip components | Power management
The power available needs to be balanced with the tasks that need to be completed on the nanocrafts. The radioisotope power sources establish the power budget in the most conservative design.
Gram-scale StarChip components | Protective coating
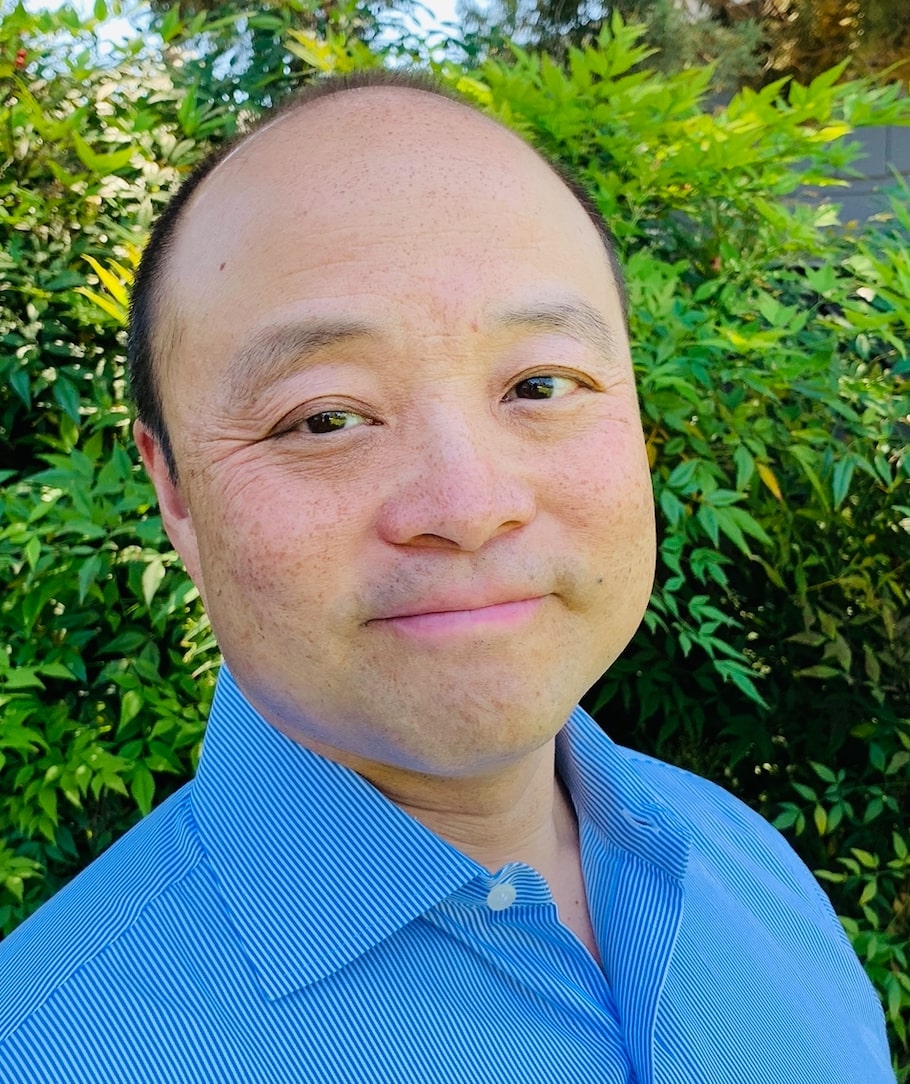
Brian Wang is a Futurist Thought Leader and a popular Science blogger with 1 million readers per month. His blog Nextbigfuture.com is ranked #1 Science News Blog. It covers many disruptive technology and trends including Space, Robotics, Artificial Intelligence, Medicine, Anti-aging Biotechnology, and Nanotechnology.
Known for identifying cutting edge technologies, he is currently a Co-Founder of a startup and fundraiser for high potential early-stage companies. He is the Head of Research for Allocations for deep technology investments and an Angel Investor at Space Angels.
A frequent speaker at corporations, he has been a TEDx speaker, a Singularity University speaker and guest at numerous interviews for radio and podcasts. He is open to public speaking and advising engagements.